Common Design Mistakes to Avoid
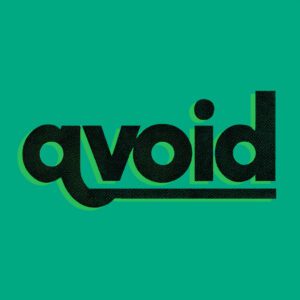
When you’re designing for laser cutting and engraving, small errors can lead to wasted materials, lost time, and lots of frustration. Whether you’re a beginner or an experienced maker, being mindful of a few key pitfalls can save you headaches — and money.
Here’s a breakdown of the most common design mistakes (and how to avoid them):
Ignoring Line Settings (Cut vs. Engrave vs. Score)
- The mistake: Mixing up cut, engrave, and score lines within your file without clearly labeling or separating them.
- Why it matters:
Your laser reads different types of lines differently. A misread line could cause the laser to cut when you meant to lightly score or engrave, ruining your project. - How to avoid it:
- Use different colors and/or layers for each operation.
- Follow your laser software’s color-coding conventions (e.g., red for cuts, blue for scores, black for engraves).
- Label your files clearly.
Incorrect or Missing Kerf Adjustments
The mistake: Designing tightly fitting parts without adjusting for the laser’s kerf (the width of material removed by the laser beam).
Why it matters: Without kerf compensation, pieces may be too loose or too tight to fit together properly.
How to avoid it:
Measure the kerf of your machine and material combination.
Adjust your designs accordingly, either by shrinking or expanding the mating parts.
Overly Thin or Fragile Elements
The mistake: Designing very thin lines, narrow bridges, or delicate features that are too fragile after cutting.
Why it matters: Small details can break during cutting, handling, or assembly.
How to avoid it:
Set minimum line thicknesses appropriate to your material.
Test small features before final production.
Unjoined Paths and Open Shapes
The mistake: Leaving open paths or unjoined shapes that should be continuous.
Why it matters:
Some lasers can’t properly interpret open paths for cutting.
The laser might pause or double-cut, leading to burns or wasted material.
How to avoid it:
Always “Join” or “Combine” paths before exporting.
Use your design software’s path cleanup or validation tools.
Using Raster Images Instead of Vectors
The mistake: Importing PNG, JPG, or other raster files when a clean vector file is needed.
Why it matters: Raster images cannot be cut — they can only be engraved (and often with lower quality).
How to avoid it:
Convert raster images to vector paths using tools like “Trace Bitmap” (Inkscape) or “Image Trace” (Illustrator).
Always export in proper vector file formats (SVG, DXF, AI, etc.) for cutting.
Incorrect Scaling or Units
The mistake: Designing in pixels, inches, or centimeters — and forgetting to convert to your laser’s preferred unit (often millimeters).
Why it matters:
Your design could end up tiny, oversized, or incorrectly proportioned.
How to avoid it:
Set your document units to millimeters from the start.
Double-check scaling when importing/exporting files.
Poor Material Planning
The mistake: Designing without thinking about material size, grain direction, or potential warping.
Why it matters:
Your design might not fit the material sheet.
Grain or warp can affect the final appearance or functionality.
How to avoid it:
Lay out designs with material dimensions in mind.
Arrange pieces with grain direction if aesthetics matter.
Use tabs or frames to keep thin materials from shifting during cuts.
Quick Checklist Before You Hit “Start”
✅ Are your cuts, scores, and engraves clearly separated?
✅ Have you accounted for kerf?
✅ Are all paths closed and joined?
✅ Are you using proper vector files?
✅ Is your design scaled correctly for your material?
✅ Are any thin parts sturdy enough for your material thickness?
✅ Did you review for unnecessary complexity?hin or Fragile Elements
Final Pro Tip:
Test First, Cut Big Later
Even pros do small test cuts before running large, complex jobs. A few minutes testing can save you hours (and expensive material).
Laser making is part creativity, part precision — and mastering both will help you create amazing, professional-quality pieces!